Technische Sauberkeit von elastomeren Dichtungen
Technische Sauberkeit von elastomeren Dichtungen im Automobilbau
Ein Konflikt zwischen Anforderungen, Dichtungseinsatz und wirtschaftlicher Umsetzbarkeit
Die technische Sauberkeit ist aus der Automobilindustrie nicht mehr wegzudenken. Downsizing, Umweltanforderungen und Gesetzesvorgaben erfordern immer leistungsfähigere und effizientere Komponenten. Die Empfindlichkeit gegenüber Schmutzrückständen steigt dadurch weiter an. Hohe Sauberkeitsanforderungen gelten auch für C-Teile. Um diese zu erfüllen, müssen meist Reinigungsprozesse eingeführt werden – mit entsprechenden Folgen.Die technische Sauberkeit ist zwischenzeitlich unabdingbar im Automobilbau. Umweltauflagen und Gesetzesvorgaben verlangen immer höheren Leistungen der Bauteile und gleichzeitig werden die leistungsfähigeren Komponenten stetig kleiner, Materialien müssen geändert werden. Als Folge steigt die Empfindlichkeit der Komponenten gegenüber Verschmutzungen, denn Partikel-Verunreinigungen können zu unterschiedlichen Schadensbildern führen. Verstopfte Ventile, Riefenbildung, beschädigte Lagerungen bis hin zu verkürzter Lebensdauer der Bauteile sind nur einige Beispiele dafür. Zunehmend werden daher viele der verwendeten Bauteile mit entsprechenden Sauberkeitsanforderungen belegt. Nicht selten sind damit steigende Kosten verbunden, die sich vor allem bei C-Teilen empfindlich bemerkbar machen können.
Umsetzbarkeit der technischen Sauberkeit für elastomere Dichtungen
Dichtungen aus Standard-Produktionsprozessen erfüllen die teils hohen Anforderungen aus der Automobilindustrie an die technische Sauberkeit zumeist nicht. Fehlende Vorkehrungen hinsichtlich sauberer Prozesse erlauben keine Bestätigung definierter Restschmutzanforderungen. Häufig werden Dichtungen für den Automobilbau in denselben Produktionsstätten gefertigt wie Industrie Standarddichtungen ohne spezifische Sauberkeitsanforderungen. Eine Umrüstung ganzer Fertigungsstätten lohnt für die Hersteller oft nicht.
Für Dichtungen werden definierte Anforderungen der technischen Sauberkeit daher in der Regel über gesonderte Reinigungsprozesse erfüllt. Sei es in der eigenen Fertigung oder aber bei Dienstleistern der Reinigungsbranche. Nasschemische Reinigung, teilweise kombiniert mit Plasmareinigungsprozessen, dient der Erzielung des erforderlichen Sauberkeitslevels.
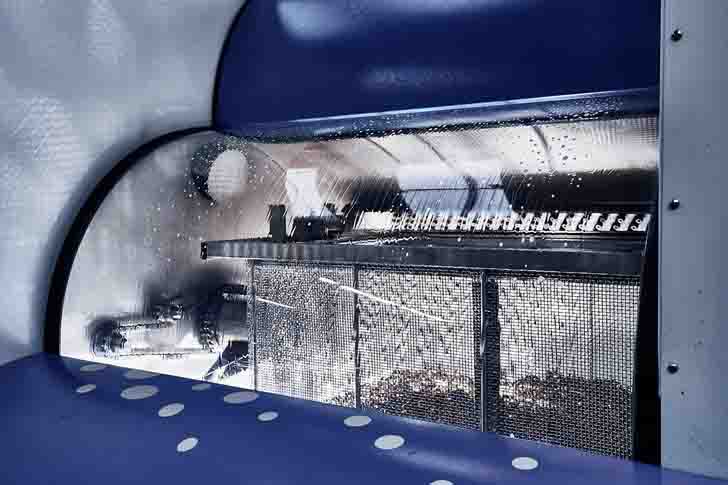
Bild 1: Reinigungsanlage Kleinteile (Quelle: APO GmbH)
Werkstoffe und Geometrien der unterschiedlichen Dichtungen setzen dabei die Grenzen der Umsetzbarkeit. Speziell die Reinigung von Elastomeren ist besonders anspruchsvoll. Anhaftende Partikel lösen sich schwer aufgrund der hohen Klebeneigung von Gummi. Ultraschall ist bei den elastischen Materialien oft nur mäßig erfolgreich. Die schwere Zugänglichkeit und geringe Größe der Dichtungen setzen in Reinigungsprozessen oft hohe Maßstäbe. Hochalkalisch oder bei hohen Temperaturen zu reinigen, bringt unter Umständen Vorteile im Reinigungseffekt. Jedoch können elastomere Dichtungen dabei beschädigt werden. Deshalb wird zumeist auf niederalkalische oder neutrale Reiniger auf wässriger Basis ausgewichen, unter Umständen mit Einbußen beim Reinigungserfolg. Doch selbst wenn effizient gereinigt wird und Grenzwerte erzielt werden können, kann nicht oder nur erschwert mit den gereinigten Dichtungen gearbeitet werden. So hat die Reinigung doch oft ungewollte Folgen.
Ungewünschte Folgen von Reinigungsprozessen
Gummi-Metall-Verbindungen mit Nicht-Edelstählen, sofern ihre Beschaffenheit überhaupt eine effiziente Reinigung zulassen, verlieren oft ihren Korrosionsschutz. Zuvor aufgebrachte Primer oder andere Schichten, die korrosionsschützend wirken, können bei Nassreinigungsprozessen teilweise oder komplett abgewaschen werden. Der Einsatz von Edelstählen oder Nacharbeiten zur Wiederherstellung eines Korrosionsschutzes sind als Folge notwendig. Nachträglich aufgebrachte, schützende Substanzen erhöhen häufig das Wiederverschmutzungsrisiko wodurch sich der Erhalt der Sauberkeit aufwändiger gestaltet. Die gereinigten Dichtungen sind dadurch oft nicht mehr wirtschaftlich.
Ähnliches gilt für reine Elastomerdichtungen, die im Regelfall nach der Produktion zumindest durch verbleibende Formtrennmittel eine leichte Schmierung aufweisen, oder gar nachträglich mit Ölen behandelt werden. Sie sind nach Reinigungsprozessen nicht nur definiert sauber, sondern auch trocken und stumpf. Die Handhabung der Dichtungen bei Einbau und Einsatz wird dadurch erschwert.
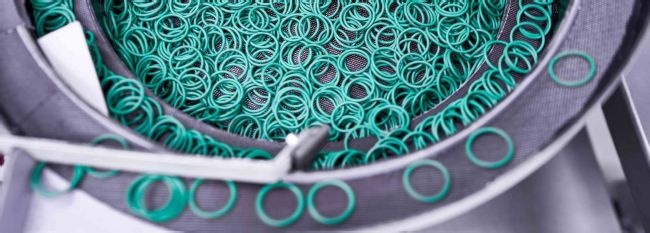
Bild 2: Vibrationswendelförderer. (Quelle: APO GmbH)
Adhäsions- und Montagekräfte von gereinigten Dichtungen sind im Vergleich zu ungereinigten teilweise um ein Vielfaches höher. Dies kann sowohl bei manueller, als auch – wie im Automobilbau üblich – bei automatischer Montage zu Problemen führen. Schon die Vereinzelung durch Vibrationswendelförderer und anschließende Zuführung der Elastomerdichtungen gestaltet sich aufwändiger als gewohnt. Die Dichtungen haften stärker aneinander und rutschen schlechter über Zuführschienen.
Bei Fügevorgängen kommt es häufiger zu Beschädigungen und Abscheren der Dichtungen. Vor allem unbemerkte Beschädigungen, die Regel bei automatischen Fügevorgängen, führen zu vorzeitigem Dichtungsausfall. Reibkräfte in bewegten Einbausituationen erhöhen sich, wenn auch teilweise in verkraftbarem Maße, so doch in unkalkulierbarer Höhe. Auf Dauer und in Summe ist der Anstieg von Montagekräften, Beschädigungsrisiko und Bewegungsenergien oft nicht tolerierbar.
Gereinigte Dichtungen also verlangen oft nach Schmierung für ihren reibungslosen Einbau und Einsatz. Bei hohen Sauberkeitsanforderungen und vor allem bei automatischer Montage verbieten sich jedoch die üblichen Fette und Öle oft aufgrund ihres erhöhten Verschmutzungspotentials.
Maßnahmen zur Beseitigung unerwartet hoher Reib- und Montagekräfte
Abhilfe können hier die bereits weit verbreiteten Gleitlackbeschichtungen schaffen. Schon jetzt sind Beschichtungen zur Verbesserung der Montagefähigkeit und Reduzierung der Reibung im dynamischen Einsatz von Dichtungen ein Standard im Automobilbereich. Doch sie bilden ein großes, oft noch unbekanntes Hemmnis bezüglich der Anforderungen an die technische Sauberkeit der Bauteile.
Für eine gleichmäßige und dünne Beschichtung von Elastomerdichtungen sind in der Regel Sprüh-Trommelverfahren im Einsatz. Die Bauteile werden in rotierenden Trommeln bei erhöhten Temperaturen mit Beschichtungssubstanz besprüht. Die Tröpfchen treffen auf die Dichtungsoberflächen und werden durch aneinander reiben der bewegten Bauteile in gleichmäßigen Schichten eingewalzt. Einige der Tröpfchen trocknen durch die erhöhten Temperaturen in den Trommeln bereits auf ihrem Weg zur Bauteiloberfläche. Auch diese werden größtenteils in die Schichten mit eingetrommelt.
Manche jedoch lagern sich, vor allem an den Bauteil-Innendurchmessern, als Partikel auf den Oberflächen ab. Diese haften fest und lassen sich meist nur teilweise durch Nassreinigungsprozesse entfernen. Sie lösen sich dagegen leicht bei Montagevorgängen – mit entsprechenden Folgen. Die Partikel werden unbemerkt in Systeme und Komponenten eingeschleppt. Da viele der genutzten Gleitlacke transparent sind, können Partikelverunreinigungen durch Beschichtungen schwer nachgewiesen werden. Auch der oft integrierte UV-Indikator hilft bei der Analyse nicht weiter.
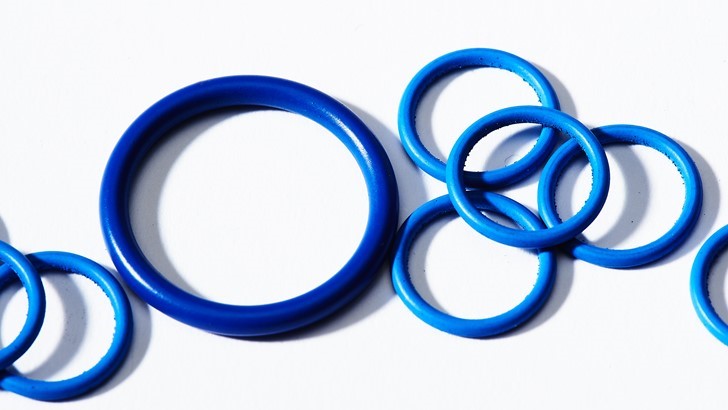
Bild 3: Beschichtete O-Ringe, Partikel am ID (Quelle: seals’n’finishing)
Es gibt durchaus Produktionsmethoden und Prozesseinstellungen, die diese Partikelgenerierung auf ein Minimum reduzieren. Auch der Einsatz von Beschichtungen aus Gasabscheidung kann helfen. Alles in allem jedoch erhöhen nicht nur die Reinigungsvorgänge selbst, sondern auch die nachfolgende Beseitigung von ungewollten Folgen die Kosten für Dichtungen, klassischen C-Teilen im Automobilbau.
Herausforderung technische Sauberkeit und Kostenmanagement bei C-Teilen
Die Erfüllung durchaus berechtigter Anforderungen an die technische Sauberkeit von Dichtungen im Automobilbau führt bereits durch zusätzliche Reinigungsprozesse und Prozessüberwachung zu erhöhtem Aufwand und Kosten. Diese können durch teilweise notwendige Maßnahmen zur Beseitigung ungewollter Folgen von Reinigungsprozessen weiter steigen.
Für ein erfolgreiches Kostenmanagement bei Dichtungen als typischen C-Teilen im Automobilbau ist frühzeitige Kommunikation unabdingbar. Das gesamte Bauteil mit allen Anforderungen sollte im Vorfeld betrachtet, entsprechend mögliche Folgen von Reinigungsprozessen beachtet werden. Ingenieure und Entwickler können kostengünstige Lösungen erarbeitet, wenn frühzeitig an alle Faktoren gedacht wird. Schon bei der Auswahl von Dichtungsmaterialien und Geometrien sollten später notwendige Sauberkeitsanforderungen bekannt sein, damit eine entsprechende Optimierung hinsichtlich notwendiger Reinigungsprozesse erfolgen kann. Dies setzt voraus, dass Einkäufer und Entwickler sich der Tatsache bewusst sind, dass Dichtungen in der Regel einen Reinigungsprozess durchlaufen müssen, um definierte Sauberkeitsanforderungen erfüllen zu können.
>> Erschienen in KGK 03/19 (Ausgabe März 2019, 72. Jahrgang) und in der DICHT! 3.2019
seals'n'finishing · Brühlstraße 17 · 72660 Beuren · (07025) 9 11 84 93 · info@seals-and-finishing.com